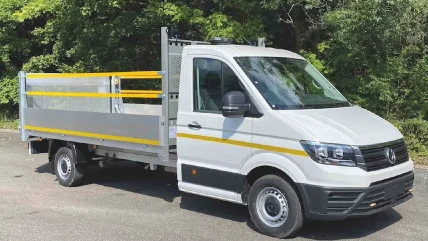
Businesses that yearn for the long-gone days when you could buy a 3.5-tonne diesel chassis with a Luton or box body and legally carry a 1.4t-load might want to consider going battery-electric. So says Anthony Clayton, sales director at Manchester-based body builder Alloy Bodies.
A steady rise in the unladen weight of diesel chassis driven in part by the burden imposed by emission control technology means that Lutons and the boxes built on them can cope with an 1,150–1,200kg payload at the very most, he says.
“That’s assuming they are constructed using composite flooring and panels,” he adds. “Have a tail-lift fitted and your payload capacity could be down to no more than 950kg to 960kg.”
Electric chassis that would otherwise be restricted to 3.5t can operate at 4.25t, however, he points out, to compensate for the weight of the battery and without any need for drivers to pass a separate driving test. The battery need not take up the entire 750kg allowance, which means the operator can enjoy a useful payload bonus.
“You can get to 1.3t or more,” Clayton says. Choose a chassis from a manufacturer that offers a choice of one, two or three batteries, such as Iveco, and specify just one, and you might be able to get up to 1.4t.
Jason Farrenden, UK operations director at body builder VFS/Scattolini, the company best-known for its tippers, says: “If you’re running a 3.5t single-cab diesel chassis equipped with one of our tipper bodies you’ll probably be able to carry no more than a tonne, maybe a bit more. That compares with over 1,200kg on an electric 4.25-tonner.”
The firm’s tippers tend to be fitted with bodies with floors made from high-strength steel and sides and tailboards made from light-in-weight aluminium with the aim of offering a mixture of durability and a respectable payload.
“We’re not getting many inquiries for electric tippers at present but we’re building a small number of electric 4.25t dropsides on Ford E-Transit chassis,” he says.
With British plants at Eastleigh in Hampshire and Wakefield in West Yorkshire, VFS/Scattolini constructs some 9,000 bodies annually in this country. Tippers and dropsides account for 80% of the volume, with the balance including Lutons.
“We build 1,200 to 1,400 Lutons a year,” Farrenden says.
Constructing some 400 bodies annually at its factory in Walthamstow, London, Tipmaster is seeing rising interest in electric tippers says managing director Matthew Terry.
“They’re starting to reach 10–15% of our volume and we’re finding we can get an electric chassis quicker than a diesel.”
He is supplying councils but the number many of them can order is limited, he says, because they don’t have the necessary charging infrastructure in place.
Going electric presupposes that you can live with the range limitations battery-electric technology imposes, as well as an eye-wateringly steep front-end price.
Says Stephen Phillips, sales manager at Clay Cross, a Derbyshire-based Advanced KFS Special Vehicles outlet: “Our product range includes car transporters and traffic management vehicles that can do 200 to 300 miles daily. Going electric won’t be a practical option for the operators concerned until the charging infrastructure improves.
“On the other hand we’re supplying 10 electric cage tippers to a local council that will operate within an 18-to-20 mile radius of their home base, and they should be fine. In fact, we’re getting a lot of inquiries about electric vehicles.”
Some businesses will go electric if they can and if it gives them a payload advantage. As indicated earlier, maximising payload involves the extensive use of composite panels, along with plenty of aluminium.
“We’ve gone for bonded construction on a lot of our products, again in a bid to save weight,” Clayton says.
While customers may be willing to pay for the materials used because of the payload advantages they bring, they also want bodies that can be repaired easily and quickly.
“Unfortunately, composites aren’t as easy to repair as GRP (fibreglass) is,” says Scott Hadley, head of sales at Aldridge, West Midland body builder J C Payne.
“If GRP gets damaged then you can fill in the hole and make it look nice,” he adds. “You don’t have to replace an entire panel.”
As well as being light in weight, strong and easy to repair, the body has to look as though it is an integral part of the vehicle. As Clayton explains, it should not be tacked on as an afterthought. That is why Alloy Bodies does all that it can to ensure that whatever it constructs blends as seamlessly as possible with the chassis and the cab, he says.
It is worth bearing in mind that supposedly identical light commercial chassis can differ to a surprising extent when it comes to their unladen weight, says Hadley. “If you have a batch of 10, then there can be a difference of as much as 50kg to 60kg between the lightest and the heaviest,” he observes.
J C Payne builds from 1,500–1,700 bodies annually, 60–70% of which are constructed on light commercial chassis. Its output at 3.5t includes Lutons, dropsides, tippers and traffic management vehicles.
Not all work is payload-sensitive. The amount of room in the cargo body and how easy it is to access may be more important considerations.
London-based Trotters Childrenswear is running an electric Renault Trucks E-Tech Master L3H1 platform cab fitted with a low-floor Luton body built by Truckcraft Bodies of Dukinfield in Greater Manchester.
With a 19.0m3 load area and a loading height of just 500mm, it delivers children’s coats, jackets, dresses, jumpers and other items of clothing to stores in the capital, including Harrods. It averages just 20–30 miles a day and its capacity has enabled the firm to reduce its two-vehicle delivery fleet to just one.
Trotters’ chief operating officer, Natasha Lunney, says: “Replacing our old polluting vans with a zero-emission electric model that is ULEZ compliant is something we’ve wanted to do for some time.”
Truckcraft also builds box, dropside, curtainsider and refrigerated bodies on light commercial chassis.
Alloy Bodies constructs 1,500–2,000 bodies annually, with 60% built on light vehicle chassis. “They’re a mixture of Lutons, low-floor Lutons, box vans and curtainsiders,” says Clayton.
Curtainsider bodies are not all that common at 3.5t, but Alloy Bodies builds 200–300 a year, he reports.
“We can build one that can carry six pallets,” he says. “Vehicles like these are being used by the pallet networks, by courier companies, and by businesses that make aircraft parts and need to transport them.”
Curtains allow the entire side of a 3.5-tonner to be opened up. That makes life easy for forklift drivers loading and unloading palletised goods – and for anybody else who needs to load and unload items quickly.
Admittedly, curtains are more vulnerable to attacks by thieves than solid body panels, but most thefts from curtainsiders involve laden trucks parked up overnight.
A laden 3.5t-curtainsider is unlikely to be parked at night at a service area or in a lay-by, says Clayton. That would not be in line with its typical usage pattern.
Customers looking to acquire a Luton or box van on a light commercial chassis but who are unsure about what they want can avail themselves of a 3D-vehicle configurator on the Alloy Bodies website. “It can be of help to salespeople at dealerships too,” says Clayton.
Everything that it configures meets type approval requirements, he stresses.
The overall supply situation is far easier than it was in the aftermath of the Covid-19 pandemic and Russia’s invasion of the Ukraine, a period during which costs escalated and shortages of some key items arose.
The economies of scale achieved by Alloy Bodies enabled it to buy materials in bulk to ensure it did not run short. “The drawback was that we had to pay premium prices”, Clayton admits.
Other major body builders have been affected by costs in the rental sector.
The reluctance of vehicle manufacturers to offer them the level of discounts on bulk purchases of chassis they were accustomed to has meant fewer orders. Volume body builders have been affected as a consequence.
The discount policy pursued by manufacturers was justified by a shortage of chassis after production lines struggled to catch up after the Covid-19 pandemic. They prioritised selling to small or medium-sized businesses to achieve better profit margins than they could obtain by selling to big fleets.
While delivery times are not back to pre-pandemic levels, chassis are now in freer supply. “So I think we’ll see manufacturers take off their self-imposed shackles early next year and start talking to the rental companies again,” Clayton predicts.
Odds are they will be encouraging the uptake of battery-electrics.
So says Phillips: “If you order an electric chassis, you’ll probably get it in 12 to 16 weeks. By contrast you could be waiting six to eight months for a diesel.”
Tipmaster does little business with the big rental fleets, claims Terry, and it is not interested in pumping out standardised products in big numbers. “There’s a lot of variation in the bodies we produce,” he says.
The company makes everything from cage tippers with bin lifts to tipping bodies designed for tree surgeons. “Most of our customers are in London, and while they might be able to get a better deal on a body elsewhere, they know that I’ll support them if they’ve got a problem,” he observes.
“We’ve got a healthy order book into the second quarter of next year, but to be honest I’m expecting a bit of a slowdown,” Terry admits.
“A lot of the builders I know are cutting back on their activities.”
They may be engaged in small developments, but they have no plans to buy large plots of land and construct major housing estates – and that has clear implications for sales of tippers and other light commercials.